Digging up and extracting the minerals needed to make electric car batteries or wind turbines comes at an environmental cost, using huge amounts of energy and dangerous chemicals and creating toxic pollution. But one Boston-area startup is getting some key materials in a different way: Instead of mining them from the ground, it uses new technology to extract them from mining waste.
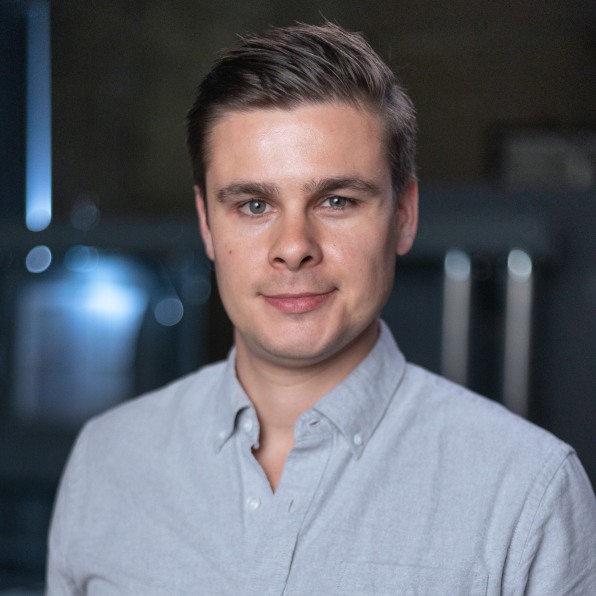
“For us, it’s about figuring out how can we extract the most from the waste that has already been mined,” says Anthony Balladon, cofounder and VP of partnerships at the startup, Phoenix Tailings. “It has already been dug out of the ground. How can we make the most of what we’ve already done, rather than dig up new holes somewhere else?”
By one estimate, there are more than 280 billion tons of global “tailings,” the sludge left behind as rocks are crushed and ground to extract metals or other minerals. Right now, mines typically don’t try to capture all of the value that’s left behind. “Traditional mines will go after one, maybe two metals in an ore source, throwing the rest away,” Balladon says. “Not because it’s not valuable, but because it’s not what they’re geared to extract—a goldmine cares about gold, they don’t care about the iron or the nickel or the rare earths that are in there.”
The company’s “re-mining” platform is designed to efficiently extract more. While the technology is proprietary, the basic process has a few steps, starting with a version of a more traditional water-based mining process that eliminates hazardous byproducts. After more processing with solvents, the approach uses electricity to separate out the metals it needs. The technology is designed to use far less energy than other methods, and can run on renewables.
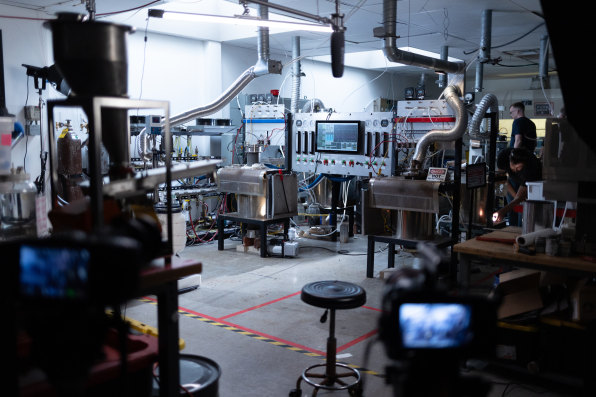
This method of reprocessing tailings can also happen in the U.S. or Europe, unlike some current mining of these materials that’s so polluting it can’t feasibly get permits. In Myanmar, where some rare-earth elements are mined now, the industry has poisoned drinking water and killed fish and other wildlife.
Car companies and others that have struggled with supply chains during the pandemic are looking for domestic sources of materials, and the Inflation Reduction Act also has incentives for U.S.-made content. “We’ve seen a big shift from from large manufacturers to shift some of their supply chains away from a single source like China or Russia,” says Balladon. “There’s geopolitical aspects to this, of course, but from a purely business standpoint, people are very much realizing that you need to have secondary and even tertiary sources of a lot of your critical supplies.”
In a pilot facility in Somerville, Massachusetts, the startup is now the only company in the U.S. producing neodymium, a key component in magnets. (While it scales up operations at a tailings facility, it’s getting the material to work for the pilot from other rare-earth producers.) With $1.2 million in new funding from the Department of Energy, it’s also working on a carbon-negative process to extract nickel, an important component in batteries. It can also produce a low-carbon form of iron that can be used to make green steel.
Now, it’s working to partner with mining companies that want to get rid of waste (and potentially, in some cases, remediate old mining land so that it can have other uses, like a park). It’s also targeting old mines where waste has been sitting for decades—or even as long ago as the 1880s. Because it starts with waste, and doesn’t have to invest in drilling into the earth, the cost of the final materials can compete with minerals from polluting mines in China and other countries.
At mines in the United States that mined materials like iron ore or copper or bauxite, “there’s the potential to satisfy a significant portion of the future rare-earth metal demand just from recovery from tailings,” Balladon says. “You would augment that with some of the traditional mines that are up and running in California, that operate at the highest level of environmental standards around the world.” The company plans to handle the first steps of its process at facilities it will set up at large mines, and then will handle the final step at centralized sites where it can also process materials from recycled batteries.
It’s critical to find better sources for materials as car companies convert to electric cars and the electric grid scales up solar panels, wind energy, and batteries. “We’re looking at ultimately how we access the metals that we need to power the shift to an electrified and decarbonized economy,” Balladon says.
To learn more about the innovative work Phoenix Tailings is doing, you can check out this informational video.
Media Contact: media@phoenixtailings.com